The Design Process and Computational Fluid Dynamics (CFD)

Working at Farr Yacht Design has been an exciting and challenging experience for me. I began my career at FYD working on hull development via hydrodynamic research for BMW-Oracle Racing. Today, my primary role, unique to FYD, is developing and advancing our in-house Computational Fluid Dynamics (CFD). CFD is becoming a fairly common term in yacht design but for most sailors its function in the design process is still a bit of a mystery. The best way to explain the utility of CFD is to describe a typical research project and expand on its role.

As shown above, the results of the filter are extremely reliant on quality of the test data. If there exists a substantial amount of error in the test results, then there is a very good probability that a sub-optimal design could be chosen. Thus any testing method requires meticulous execution and exhaustive validation.

Test data is best validated by confirmation from two or more completely different sources. A well funded research project utilizes both tank testing and CFD techniques to ensure realistic results. Often, we use tank tests to confirm CFD data, but the validation of both techniques is independent of one another. In the tank, typically a model is tested at some fraction of the full scale design. Thus forces and moments recorded from the model must be scaled to a full scale prediction. Unfortunately, scaling is not often a trivial operation. Usually, many iterations of scaling forces and moments are required to produce realistic results. In general, these results are confirmed by subjective review of polar data from the VPP.
CFD is calibrated much differently than tank testing. The full scale geometry is often tested to avoid the before mentioned model scale effects. Thus validation is only conducted by changing the geometry that defines the problem, the boundary conditions that govern the problem, and/or conditionals that control the problem.
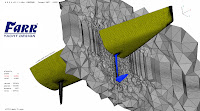
Boundary conditions and conditionals are fundamental to validating CFD results. Most mathematicians would agree that defining appropriate boundary conditions is the most difficult step in solving numerical methods. For this reason, our CFD resources include both academic and commercial codes developed from vastly different boundary treatments. We work directly with universities and other organizations to remain on the forefront of new code development. We rely on only the most experienced fluid dynamics professionals who maintain a clear understanding of numerical error when tuning codes to produce the most convergent solutions.

The single largest difference between tank testing and CFD is the ability to visualize the physics of the problem. Techniques exist to trace particles, capture the free surface profiles, and record pressure and shear information in tank testing, however such devices are fickle, setup is often ‘a priori’, and implementation is expensive. CFD offers a more complete picture of these physics by virtue of the equations being solved. As previously mentioned, the nodes of the mesh contain all the information necessary to visualize the fluid domain. The shape’s influence on the flow is easily compared using special plotting techniques. New concepts and ideas can be realized by looking at different operating conditions and comparing different designs.
In all, research of performance yachts hinges on good scientific practice and design experience. We still require more than one tool to accurately predict a yachts performance. We require the most talented experimental and theoretical hydrodynamic and aerodynamic professionals in the industry to ensure the very best test results.
-Bryan Baker, Naval Architect
2 comments:
Bryan - great article - thanks. I looking at the keel on my Farr designed Beneteau First 36.7, I notice that the aft portion of the keel is actually slightly concave in nature. Usually keels are slightly convex throughout. Is this a new development in keel shape? Was this a result of CFD design work? What is the effect on the yacht performance? Many thanks.
Hi,
My name is Pierre Orphanidis and I'm the editor of Valencia Sailing. I just discovered the FYD blog and some of the articles are extremely interesting.
Would it be possible to reproduce them on Valencia Sailing, with full credit OF COURSE?
Regards,
Pierre
Post a Comment